Methods and technologies for cementing wells: how to prepare and pour grouting mortar
After drilling a well in loose sandy soils, a stage begins aimed at strengthening the casing pipes. At the same time, the trunk should be protected from damage, aggressive groundwater, corrosion and other negative phenomena. This is a process such as cementing wells.
Carrying out cementing work on your own is quite difficult, but possible if you have knowledge about the technology of the event. We will tell you about why cementing is necessary and what you need to pay attention to when performing work. For clarity, the material contains thematic photos and videos.
The content of the article:
Why cement a well?
Well cementing is a process that follows immediately after completion. drilling operations. The cementing procedure consists in the fact that cement slurry is introduced into the annular or annular (if the casing is in turn placed in a wider polyethylene pipe), which hardens over time, forming a monolithic well bore.
Cement mortar in this case is called “grouting”, and the process itself is “plugging”. A complex engineering process, called well cementing technology, requires certain knowledge and special equipment.
In most cases, water sources can be tamped with your own hands, which is much cheaper than attracting specialists.
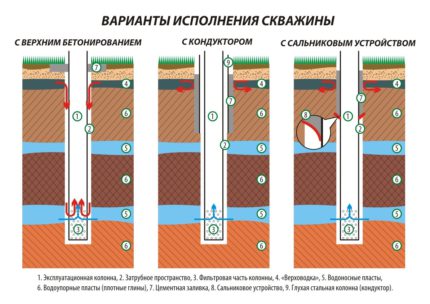
Properly performed plugging of wells into water contributes to:
- ensuring the strength of the well structure;
- well protection from groundwater and high waters;
- strengthening the casing and protecting it from corrosion;
- increase the life of the water source;
- elimination of large pores, voids, gaps through which unwanted particles can enter the aquifer;
- displacement of the drilling fluid with cement, if the first was used during drilling.
The quality of produced water and the operational characteristics of the well will depend on how well cementing is carried out. Cementing is also done for abandoned wells that will no longer be exploited.
Water source cementing steps
The whole cementing process consists of several stages, each of which has its own nuances:
- Preparation of cement slurry to fill the annulus.
- Supply of prepared cement to the well.
- Injection of grouting mortar into the annulus.
- Hardening period of cement mortar.
- Quality control of cementing.
Each stage requires the use of certain tools and special equipment. The calculations of the necessary materials are best done before the start of grouting, because the plugging process should last continuously and if, for example, you do not have enough cement mortar, then this will negatively affect the quality of cementing. We will consider the most important stages in more detail.
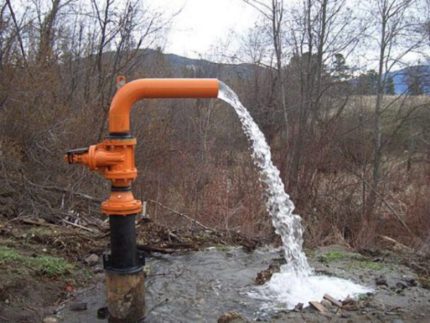
Stage number 1 - equipment preparation
All work on cementing aquifers must be carried out strictly in accordance with technical requirements, the violation of which will lead to poor-quality cementing.
When embarking on well plugging, you should know that this is an irreversible process; it is impossible to fix anything after the filing of the solution into the annulus of the well, therefore, preparatory work, namely, preparing the grout for cementing and equipment selection, must be approached as responsibly as possible!
The easiest and most effective way is to rent equipment on a vehicle platform. Such a complex will be able to prepare a cement mortar and pump it into a well under pressure, while a powerful automobile engine serves as a source of energy for the equipment.
If it is not possible to use units based on a special vehicle, then you will need:
- mixer for the preparation of cement mortar;
- high pressure pump, pumping the solution to the well;
- cementing head for injecting the solution into the well;
- filling plugs (the amount depends on the cementing method);
- various small equipment (hoses, measuring tanks).
As a hose, many experts recommend using a flexible fire hose instead of traditional HDPE pipes with a diameter of 32 cm. It is flat and passes perfectly into the annulus, providing an efficient solution flow.
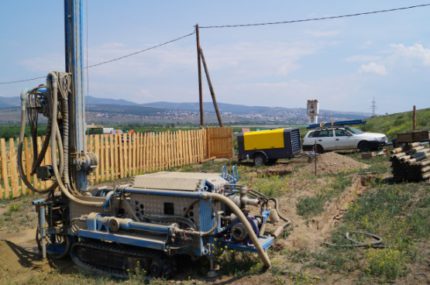
Stage number 2 - preparation of the solution
The cement slurry for cementing the well must meet a number of requirements and have:
- high adhesive properties with surfaces of any type;
- high strength after solidification, resistance to mechanical stress;
- ductility and good fluidity to fill all cracks and voids;
- chemical neutrality with respect to plugged soil layers;
- resistance to erosion by groundwater;
- lack of shrinkage during hardening.
Also, the solution must have such a consistency that it can be delivered without problems to the well and injected. The solution must be well washed off the equipment, not be chemically aggressive against it and have a minimum loss coefficient during transportation to the well.
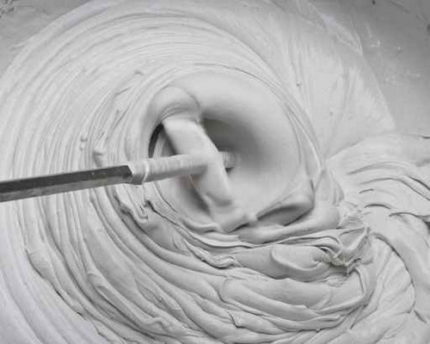
The process of preparing a cement mortar for plugging consists in uniformly mixing the components that make up it, followed by pouring water into it, with special additives previously dissolved in it.
The simplest solutions that you can prepare yourself are:
- Portland cement + quartz sand (1: 1) + special additives and water until the desired consistency is obtained. Such a solution has a low density, and its preparation is difficult, because sand included in the composition often precipitates and the use of a solution becomes impossible.
- Portland cement + barite (1.1: 1) + special additives and water. The disadvantage of this solution is its low strength.
- Portland cement + filler. Asbestos (on sandy soils), fibrous materials are used as a filler.
For the preparation of a cementitious mixture it is best to use grouting Portland cement, which is a type of silicate-based cement.
Such cement, of course, is more expensive than regular Portland cement, but its strength characteristics are much higher than that of ordinary. Barite is a heavy mineral that increases the density of the solution. Barite can be purchased at a hardware store selling bulk building materials.
By special additives that are part of cementitious mortars, we understand various substances that give the solution special properties.
These include:
- setting accelerators cement (calcium chloride, soda ash, potash), used if cementing occurs at a temperature below +5 degrees;
- setting retardersused to prevent rapid hardening (these are calcium or sodium chlorides, sodium nitrite, etc.);
- plasticizers for optimum viscosity (polymer modifiers);
- frost-resistant additives (organosilicon compounds, coupled with plasticizers);
- moisture absorbing additives (substances obtained from compounds belonging to the groups of sugar, citric, tartaric and tetraoxyadipic acids), etc.
Special additives are mixed in water, which is subsequently used for the preparation of cement slurry. Mix the solution using special machines - mixers. Sometimes manual kneading is allowed, but it requires some skill and a lot of labor.
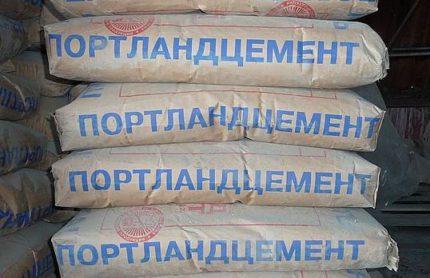
Stage number 3 - pouring the solution into the well
The main methods of cementing wells are:
- continuous or single-stage;
- two-stage;
- cuff;
- the opposite.
All methods of cementing water wells are based on one principle - pumping grout into the annulus. At the same time, the choice of cementing technology depends on specific conditions: soil type, well depth, casing material, climatic and hydrogeological conditions of the area.
The selected technology of well plugging into water should provide:
- filling the solution with the entire well alignment to the entire depth;
- completely displace flushing fluid (if any);
- creation of high-strength cement stone resistant to physical, mechanical and chemical influences;
- high rate of adhesion with soil walls of the well, casing pipes.
For deep wells, segmental cementing is used, i.e. not the entire well stem is cemented at once, but only its individual segments.
This process is very complex and practice shows that it is almost impossible to do it yourself. Therefore, we consider in more detail the technology of one- and two-stage and cuff cementing.
One-stage or continuous cementing
This method is most often used for cementing domestic aquifers. During its implementation, the cementitious solution is pumped into the annulus.
The solution is pumped under pressure using equipment that is installed on the platform of a special vehicle or stationary near the well. The cementitious mortar, under its own weight, moves to the casing “shoe” base, filling all the annular cavities.
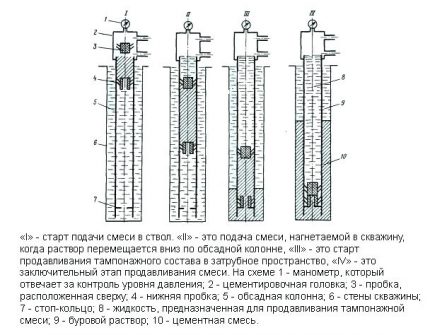
Before starting cementing well flushingand then the lower plug is introduced, which will act as a limiter. The concrete pump is turned on and the plugging solution begins to pump, under the influence of which the cork is lowered until it reaches the “shoe” of the casing.
After the injection of the mortar, the upper plug is installed and the cement mixture begins to compact until the upper plug abuts the lower one. This will mean that the solution filled the entire annulus. The compaction is carried out by means of a vibropress by pumping the mortar with a concrete pump.
The cemented well is left at rest for 36-48 hours for complete solidification of the solution. This method is only suitable for shallow, well-shaped wells. The disadvantage of this method is the inability to track the moment when the cement slurry reached the bottom of the well.
Two-stage priming system
This cementing method has been developed for oil industry wells. Due to the fact that it requires the use of serious industrial equipment (a powerful concrete pump), it is not often used in the construction of wells. Two-stage cementing is used in the following cases:
- cement mortar sets so fast that cementing cannot be completed in one cycle;
- when you want to highlight two sections in the annulus, which are separated by a significant distance;
- with a large depth of the well, when it is impossible to carry out work in one cycle.
In other cases, the use of a two-stage method is impractical due to the length of the process and economic indicators.
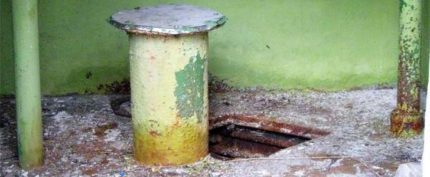
The principle of two-stage cementing is based on the fact that cement is pumped into the annulus in two stages.
The first portion of the grout is loaded and squeezed.The lower plug is lowered, which, by the action of the solution, the plug drops to the bottom. The second portion of the solution is pumped in 12-36 hours, after the final hardening of the first portion.
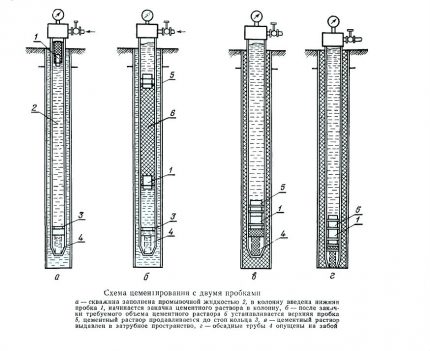
The use of the cuff method
This cementing method is used if only the top of the well needs to be strengthened. In this case, the initial task will be to determine the level to which cementing will be performed.
The level is noted on the casing by installing a special cuff. The lower part of the alignment is reliably protected by the cuff from penetration of the plugging solution.
The solution is pumped in exactly the same way as with single-stage cementing. A cuff method is used if the upper part of the well is located on sandy soils and the lower part is on clay soils. This is rare enough, so this method has not found wide application.
Cement stone formation process
The process of formation of cement stone begins immediately after the injection of the plugging solution and lasts from 12 to 36 hours. The main factors affecting the duration of the solidification of the mortar to the state of the cement stone:
- properties of the components that make up the solution;
- soil, casing material;
- hydrogeological and climatic conditions on the site;
- density of injection, correct implementation of the plugging process.
During the solidification period, it is necessary to leave the well at rest. It is forbidden to use cables, crowbars, wire to assess the quality of cementation, as this may disrupt the integrity of the resulting cement stone.
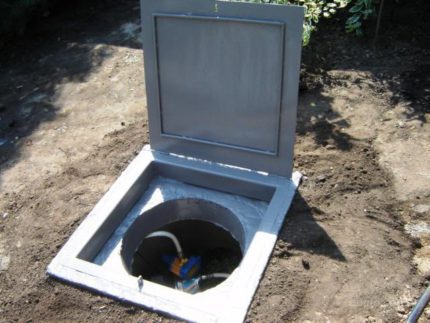
Cementing Quality Assessment
It is worth noting: despite the fact that assessing the quality of cementing of aquifers is a very important stage, it is impossible to conduct it yourself.
For its implementation, special laboratory equipment is required, which is very rare even for organizations that are engaged in drilling.
If you still intend to evaluate the performed plugging, you can order the quality control service in one of three ways:
- acoustic, based on tapping the walls of the casing, followed by processing of the data by computer programs;
- radiological when measuring with radio devices;
- thermal, based on the principle of measuring the released heat during the hardening of the cement mortar.
At home, you can use the simplified thermal method by measuring the temperature at the walls of the well. When it reaches the ambient air temperature and becomes 0.5-1.5 degrees lower, then we can talk about complete solidification. However, even after this, it is recommended to wait 2-3 days and only then bring the well into operation.
After the test is completed, the wellhead is cleaned from cement slurry using bastards. Then a leak test is performed, for which high pressure water is pumped into the well pipe for 30 minutes. The tightness criterion will be a pressure drop of about 0.3-0.5 MPa. The well is now fully ready for use.
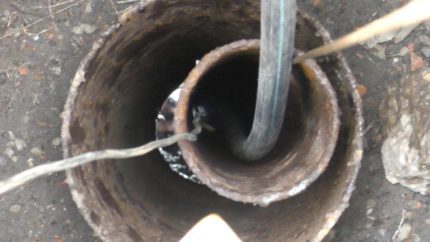
Conclusions and useful video on the topic
In the videos below, we are talking about wells in the oil and gas industry, but the principle of the production technology is the same as for aquifers.
Single-stage cementing procedure:
Cuff cementing production specifics:
Technological features of two-stage cementing:
Cementing is a complex process that requires the use of specialized equipment. However, this does not mean that it is impossible to conduct it yourself. By choosing and correctly preparing the grouting mortar, using the minimum set of aggregates, it is quite possible to cope with the work yourself.
In any case, the operation of the well without cementing the well will not be long, and the cost of drilling a new water source will be no less.
If after studying the material you still have questions about how to properly cement the well after drilling, or you have valuable knowledge on this issue, please leave your comments in the block below.
The plugging process should be taken into account when calculating the cost of drilling, so as not to overpay later. It is necessary to contact the organizations that were involved in drilling the well: they have reports on the work performed with the geological and hydrogeological sections built in the area, they know how to properly go through and plug the well, and not do everything at random. Unfortunately, now everyone who is not lazy is engaged in drilling, even without approximately knowing the properties of soils and the depth of the aquifer.